As we all know, there are various adhesives on the market, and different adhesives have different uses.
When we choose adhesives, do we understand adhesives?
Can you choose the adhesive product that best meets your requirements?
I hope that after reading the article Skills That You Can Learn From Adhesive, it will help you in the future.
Definition of adhesive
A class of natural or synthetic, organic or inorganic substances that can connect two or more parts or materials through the adhesion of the interface and the cohesion of substances, collectively referred to as adhesives. It is called glue.
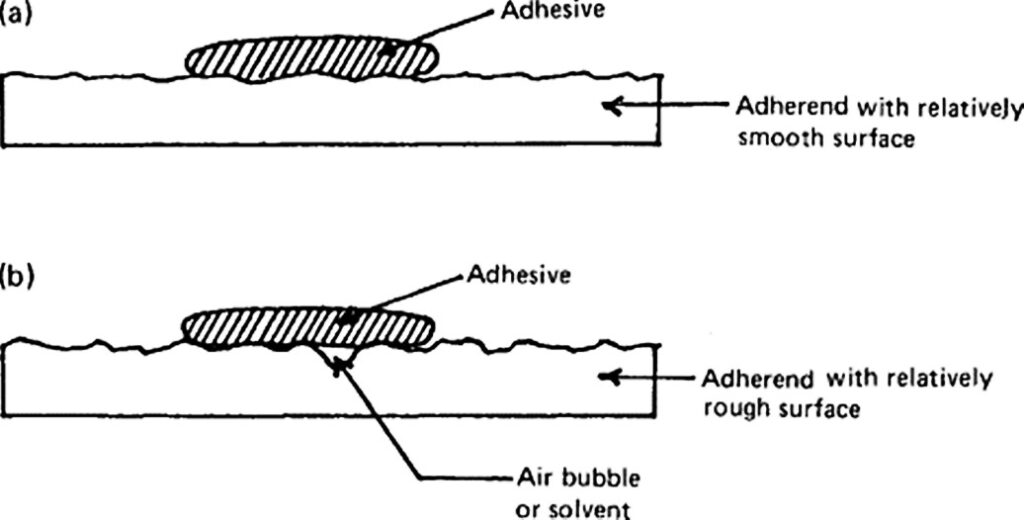
- Adhesion refers to the state in which two surfaces are joined together by chemical force, physical force, or both.
- The adhesive must first adhere to the surface of the adherend, which is due to the adhesive force between the two phases, which originates from the secondary or primary bond force.
Cohesion: that is, the state in which the particles within a single substance are bound together by primary valence bond forces (including ionic bonds, covalent bonds, coordination bonds, metal bonds, etc.) and secondary valence bond forces (including van der Waals forces and hydrogen bonds).
The cohesive force of the adhesive is related to factors such as intermolecular force, relative molecular mass, degree of cross-linking, crystallization, and molecular entanglement.
Requirements for Adhesives
- Regardless of the state, it should be in a liquid state when applied.
- It can completely spread and fully wet the surface of the adherend.
- It must be able to transform the liquid into a solid or gel state in some way to form a tough and stable adhesive layer.
- After curing, it should have a certain strength. Able to connect reliably, transmit stress, and resist damage.
- It can withstand temperatures above 0 °C and withstand the test of a certain period.
Classification of Adhesives
Classified according to appearance: solvent-based emulsion type (water-based) (eg: white glue); paste or paste (eg: silicone sealant); solid type (eg: epoxy putty); film type (eg: glue dots).
According to the curing method: water-based evaporation type (eg: white wood glue), solvent evaporation type (eg: Alcohol glue, neoprene glue), hot melt type(eg: hot melt glue sticks ), chemical reaction type(instant super glue), pressure sensitive type(removable glue dots).
The components of the adhesive are as follows:
Binder | Hardener | Solvent | Plasticizer | Filler | Coupling agent | Cross-linking agent | Accelerator |
Toughening agent | Tackifier | Thickener | Thinner | Anti-aging agent | Polymerization inhibitor | Flame Retardant | Initiator |
Photosensitizer | Defoamer | Preservative | Stabilizer | Complexing agent | Emulsifier |
The type of binder:
The binder is the main component, or main polymer of the adhesive, which plays a role in bonding.
According to the different chemical compositions, the source of the base material is inorganic compounds and organic compounds. Organic compounds are polymer binders for polymer synthesis.
- Commonly used organic compounds: thermosetting synthetic resins: phenolic resins, epoxy resins, amino resins, polyurethane resins, unsaturated polyesters, and acrylic resins.
- Thermoplastic synthetic resin: rubber base material, natural polymer material, water-based latex, base material.
- Rubber base adhesive.
The selection principle of the adhesive base material:
The selection is according to the object of the adhesive application, the application occasion, and the application performance. At the same time, there is a close relationship between the molecular structure of the molecular binder and the adhesive properties.
- The polarity of polymer materials is related to
- Crystallization properties of polymer materials
- Molecular weight of polymer materials
Curing agent (hardening agent):
The raw material in the ground state is transformed into a linear polymer or a network polymer through a chemical reaction, polymerization, polycondensation, or cross-linking reaction. It is a substance with mechanical strength and stability of the adhesive joint.
Choice of hardener:
- It is best to be a liquid non-toxic, colorless, and odorless substance.
- The reaction between the curing agent and the cured material should be stable and the heat release should be less to reduce the cohesion of the adhesive layer.
- Heat resistance, choose a curing agent with more reactive groups in the molecule.
- Toughness, choose a curing agent with a longer molecular chain.
Adhesive solvent:
refers to a liquid that can reduce the intermolecular force of certain solids or liquids, so that the dissolved substances can be dispersed into a molecular or ionic homogeneous system. The commonly used solvents are low-viscosity liquid substances.
There are mainly aliphatic hydrocarbons, aromatic hydrocarbons, halogenated hydrocarbons, esters, alcohols, ketones, acids, ethers, terpene olefins, amides, and water. However, most organic solvents have certain toxicity, flammability, explosiveness, pollution to the environment, hidden dangers to safety, and harm to the human body.
The role of the solvent:
- The medium of the polymerization reaction: the reaction is moderate and the temperature is easy to control.
- Dissolving base material: preparing solvent-based adhesive.
- Diluent: dilute the adhesive to make it reach a certain viscosity, which is conducive to wetting and easy to coat.
- Adjust the volatilization rate of the adhesive.
- Prevent gel to increase storage stability.
- Surface cleaning agent before bonding.
- Direct bonding, some plastics.
- Reduce costs and improve efficiency.
Choice of adhesive solvent:
- Polarity: choose a solvent with the same or similar polarity as the base material (the principle of similar compatibility).
- Solubility parameter (related to polarity): the solubility parameter of the solvent is similar to that of the polymer matrix.
- Volatility of the solvent: choose a solvent with appropriate volatility or a solvent mixed quickly and slowly. The solvent evaporates too fast: the surface of the glue is easy to form a film, and the solvent under the film is not easy to volatilize; the solvent evaporates too slowly: the surface drying time is slow, which affects the work efficiency.
- The choice of solvent should take into account price, toxicity, and source.
The role of softener:
It is an essential component of SBS, its role is to adjust hardness, fluidity, and reduce costs. Oil-filled SBS can make compounding and processing easier.
The most commonly used is naphthenic oil. Aromatic hydrocarbons are dark in color, poisonous, and cannot be used. Paraffin oil can not improve physical properties, and will also lead to spraying.
Types of softeners: According to the composition of hydrocarbons, they are divided into three categories: paraffin, cycloalkyl, and aromatic groups.
Features of softener:
- Paraffin-based rubber oil: good oxidation resistance and light stability, but relatively poor emulsification, compatibility and low-temperature.
- Naphthenic rubber oil: has the advantages of paraffin base and aromatic base, moderate emulsification and compatibility, no pollution, no toxicity, and a wide range of applications.
- Aromatic rubber oil: good compatibility, large filling amount, low price, and high strength of the rubber product obtained. But the color is dark, toxic, and pollutes the environment.
Definition of plasticizer: It is a substance that reduces the glass transition temperature and melting temperature of polymer compounds, improves the brittleness of the adhesive layer, and enhances melt fluidity.
The role of plasticizers:
- Disperse the active groups of polymer compounds, and weaken the intermolecular force, thereby reducing the interaction between molecules.
- Increase the heat, elongation, and cold resistance of the polymer compound, reduce its cohesive strength, elastic modulus, and heat resistance.
Choice of plasticizer:
- Polarity: The size of the polarity affects the compatibility of the plasticizer and the host material, and its principle is the same as that of the solvent.
- Persistence: The physical and mechanical properties of the glue are affected by the loss of exudation, migration, and volatilization. Choose high-boiling or high-molecular-weight plasticizers.
- Molecular weight and state: the higher the molecular weight, the better the bonding strength.
Commonly used plasticizers:
phthalates, phosphates, adipates, and sebacates, etc. Definition of filler: A solid material that does not chemically react with the matrix in the adhesive, but can change its properties and reduce costs.
Commonly used fillers are divided into organic fillers and inorganic fillers:
Organic fillers – improve the brittleness of the resin, high hygroscopicity, and low heat resistance;
Inorganic fillers – increase the relative density and brittleness of the glue, but improve heat resistance, media properties, shrinkage, etc.
Choice of fillers:
- Inactive and does not react with other components of the adhesive.
- Good dispersibility and good wettability of the base material.
- Does not contain moisture, harmful substances, grease, and no hygroscopicity.
- Uniform particles, non-toxic.
- Wide range of sources, convenient processing, and low price.
- The density of the filler should not be too different from the density of the base material.
- Appropriate dosage.
Commonly used fillers:
silica, calcium carbonate, magnesium carbonate, aluminum powder, phenolic resin, etc.
Coupling agent:
a compound that can produce a certain binding force with polar substances and non-polar substances at the same time, which is characterized by a substance with both polar and non-polar parts in the molecule.
Commonly used coupling agents are organic chromium coupling agents, organic silicon coupling agents, and titanate coupling agents. Commonly used in adhesives are silane coupling agents.
The role of the coupling agent:
- Increase the intermolecular force of the host resin itself and improve the cohesive strength of the adhesive.
- Increase the bond between the resin and the adherend, and play a certain role in bridging. Different coupling agents have different reactive groups and different reactive groups have different effects on bonding properties.
Initiator:
a substance that can decompose and generate free radicals under certain conditions. Generally, an initiator is added to a compound containing an unsaturated bond. Commonly used initiators are dibenzoyl peroxide, cyclohexanone peroxide, isopropyl peroxide, benzene, azobisisobutyl cyanide, etc.
Accelerator (catalyst): A substance that can reduce the decomposition temperature of the initiator or accelerate the reaction between the curing agent and the resin rubber.
Anti-aging agent:
a substance that can delay the aging of polymer compounds. For the adhesive used under high temperature and exposure, it is easy to deteriorate due to aging, so add an anti-aging agent when compounding.
Thickener:
A low-viscosity adhesive that adds substances that increase its viscosity
Polymerization inhibitors and stabilizers:
substances that prevent or delay the self-crosslinking of polymers and monomers containing unsaturated bonds during storage (hydroquinone).
Through the above content, we know what is an adhesive and its components, and what are the properties and uses of this all-purpose adhesive.
Below are the top ten bonding functions of adhesives for your reference.
1. Instant bonding
Instant glue is a one-component cyanoacrylate, transparent, fast-curing adhesive at room temperature. It has the characteristics of fast curing and high bonding strength. The tensile force of the iron piece bonded with Hopson cyanoacrylate super glue is enough to lift a 5KG iron block.
2. The bonding of structural parts
Structural Adhesive: This is an adhesive used to bond high-strength materials such as wood, composites, or metals with a practical bond strength greater than 6.9Mpa (1000psi) at room temperature.
Structural adhesives are known for their high strength, excellent peeling resistance, impact resistance, and simple construction process. They are suitable for bonding various materials, including metals, ceramics, plastics, rubber, wood, etc.
Structural adhesives are widely used in engineering, primarily for construction reinforcement, anchoring, bonding, and repair tasks. Such as bonding steel, bonding carbon fiber, hole repair, crack reinforcement, sealing, etc.
3. Liquid seal plugging
Liquid sealant, also known as a liquid gasket, liquid gasket, or liquid sealing packing. It is a fluid liquid at room temperature. It is applied to various connections or parts that need to be sealed to form an elastic glue layer, which can replace the usual gasket and play a sealing role.
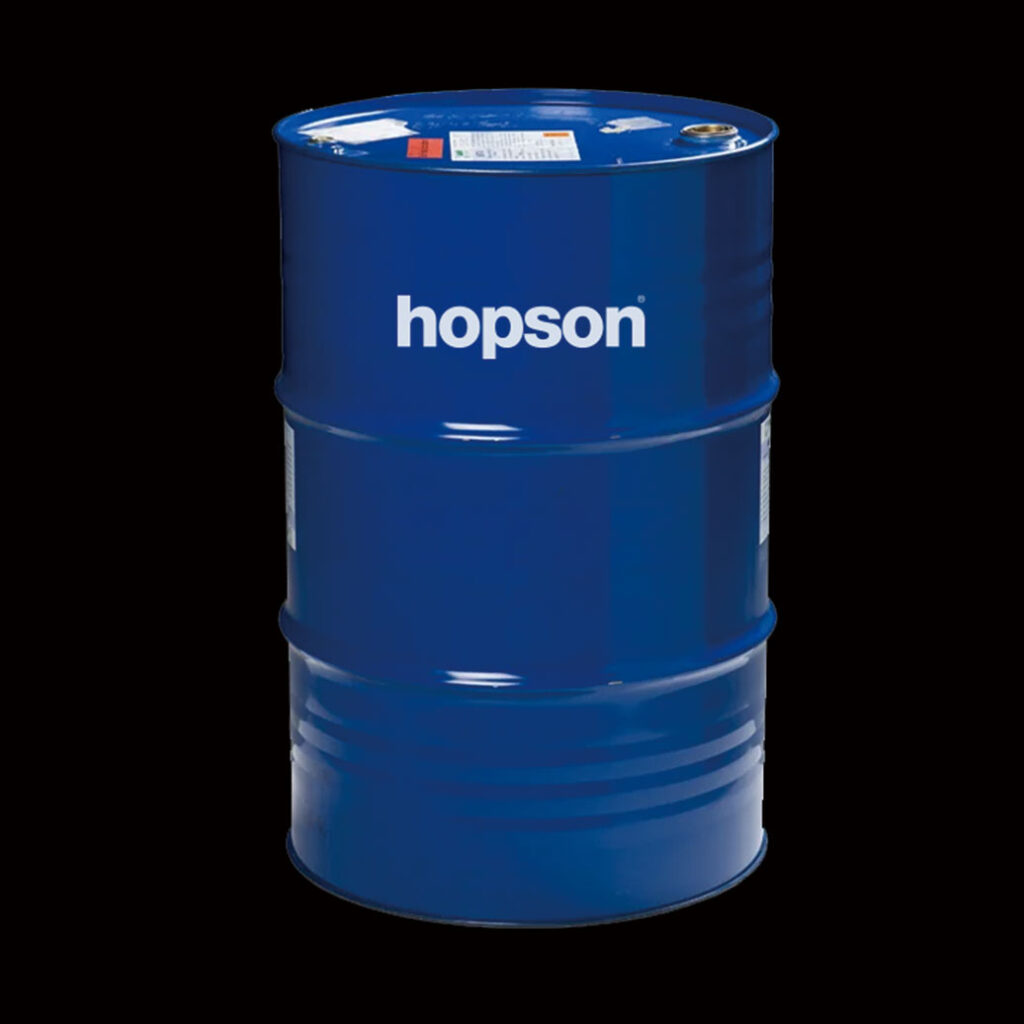
4. Underwater bonding
Underwater adhesives, also known as water-absorbing adhesives, are adhesives that can be bonded in water. Ordinary adhesives can only be used in dry conditions, such as in water or wet conditions, the bond strength will be greatly reduced. The underwater adhesive can be bonded in water. For aquarium maintenance, the hull and bottom holes can be repaired directly underwater, which is very convenient.
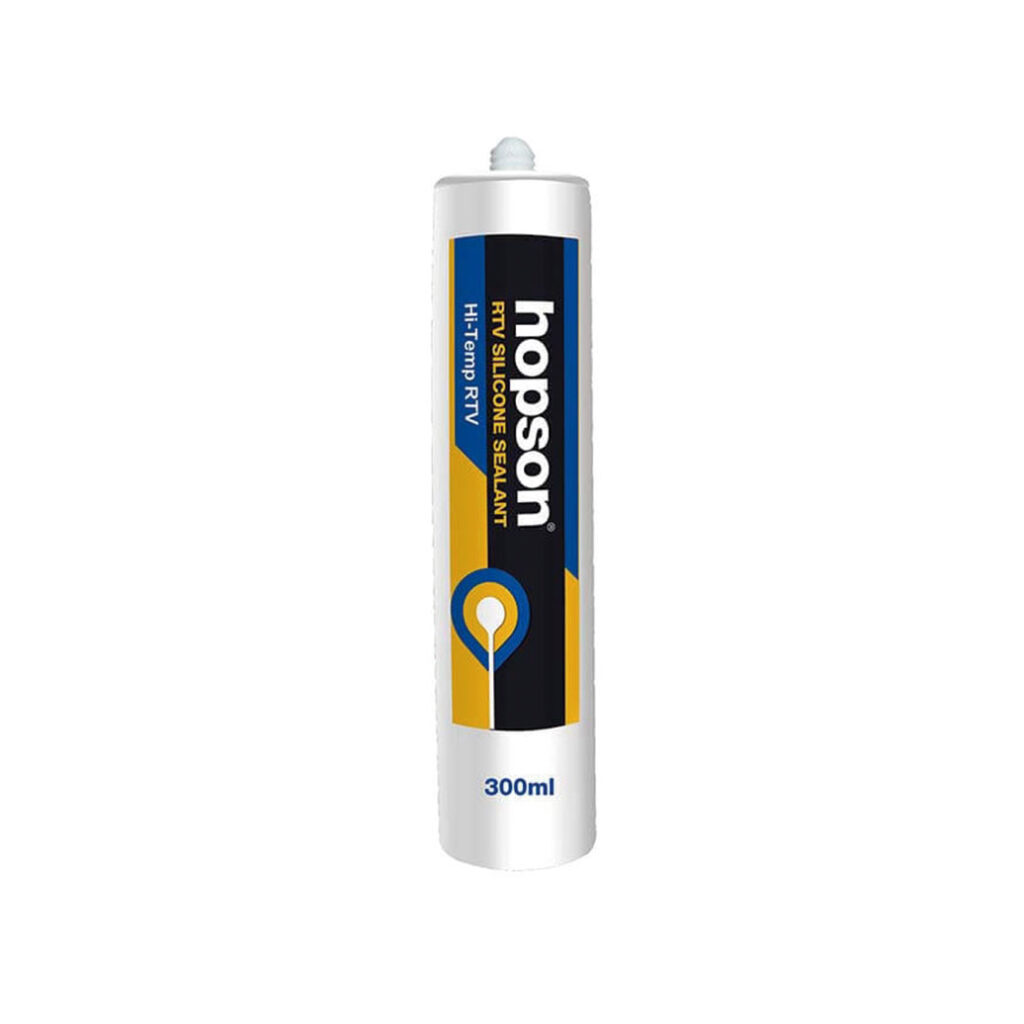
5. Hot melt bonding
Hot-melt adhesive is a solid, it can only be glued after being heated and melted into a fluid, and it will return to a solid after the bonding is cooled to form a firm bond. Hot melt adhesives are formulated with thermoplastic polymers and tackifiers.
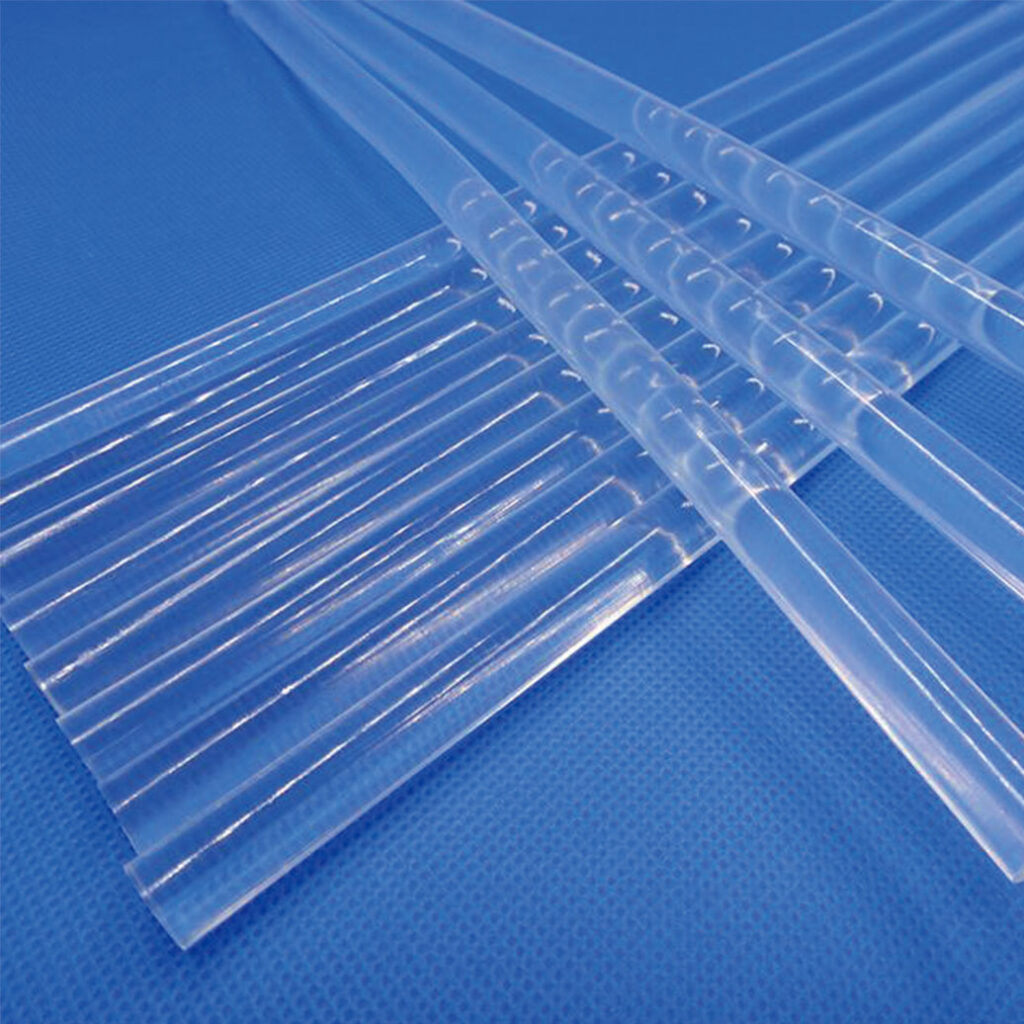
6. Oil surface bonding
Oil surface adhesive, the adhesive is applied to the bonding surface with oil, the oil is absorbed and diffused by the adhesive, and does not affect the bonding force. This glue is called oil surface adhesive or oil-absorbing adhesive.
The glue for the oil surface does not need to be degreased on the surface first, which simplifies the process and has good bonding strength.
7. high-temperature bonding and ultra-low-temperature bonding
General adhesives can withstand temperatures below 100°C. Inorganic adhesives can withstand about 600 ℃, of which ceramic adhesives are the best, which can withstand high temperatures of 1300 ℃. The ultra-low temperature resistant adhesive can maintain high strength and toughness at -196℃, or even low temperature at -269℃.
Hopson® adhesive manufacturer can customize the adhesive according to your requirements, please send us your parameter requirements.
This product is designed for pasting commodity labels, sealing cartons, bundling wire harnesses, and protecting the surface of high-gloss metal plates. It is available in various forms, such as glue dots and adhesive tapes, making it versatile for different applications.
9. Medical bonding
Medical super glues for cuts encompass a range of formulations tailored for different applications, including soft tissue adhesives, dental adhesives, orthopedic adhesives, and skin pressure-sensitive adhesives. These adhesives play a significant role in various medical procedures, such as skin and wound adhesion, blood vessel repair, tubular digestive tract reconstruction, tracheal anastomosis, and partial resection surgery of organs like the liver, kidney, pancreas, and spleen.
PerfectSeal is a professional manufacturer of surgical glue for wounds. This medical tissue glue has obtained a CE certification. PerfectSeal’s tissue adhesive is suitable for sealing wounds in humans and pets, circumcision, and pet sterilization surgeries.
10. Conductive bonding of electronic devices leads
In addition, there are conductive adhesives for electronic device leads. High-transparency optical glass adhesive for optical glass bonding light-sensitive photosensitive curing adhesive electron beam curing adhesive, etc.
It can be seen that the many uses of adhesives not only bring a variety of conveniences to life but also improve efficiency and save costs for industrial production. The following are some tips when choosing an adhesive, I hope it can help you.
Precautions when choosing adhesives
1. Storage period
- Each product has a storage period. According to international and domestic standards, the storage period refers to normal temperature (24°C). Acrylic glue is 20 ℃.
- For acrylic products, the higher the temperature, the shorter the storage period.
- For water-based products, if the temperature is below minus 1°C, it will directly affect the product quality.
2. Strength
- There is no all-purpose glue in the world. It is best to use a special adhesive for different adhesins. You can send us your requirements and we will choose the most suitable adhesive.
- If the strength of the adherend itself is low, then it is not necessary to choose high-strength products, otherwise, unnecessary excessive capacity and increased costs.
- Not only high initial strength but also durability.
- The performance of high-temperature curing adhesive is much higher than that of room-temperature curing. If high strength and good durability are required, high-temperature curing adhesive should be used.
- For a cyanoacrylate glue (502 super glue), in addition to emergency or small area repair and continuous production, for materials requiring high bonding strength, Hopson original glue can be used.
3. Other Tips
- White latex and urea-formaldehyde glue cannot be used for sticking metal.
- For transparent adhesives, you have several options, including polyurethane glue, optical epoxy glue, saturated polyester glue, or polyvinyl acetal glue which can be chosen based on specific needs and applications.
- The adhesive should be non-corrosive to the adherend. For example, polystyrene foam boards, can not use solvent-based neoprene adhesive.
- Adhesives with high brittleness should not stick to soft materials.
4. Precautions when using AB glue
- For the adhesive of the AB component, please mix it according to the requirements of the manual.
- For the AB component adhesive, it is crucial to thoroughly mix the components before use, as failure to do so may prevent the adhesive from curing properly.
- The adherend must be cleaned without moisture (except underwater curing glue).
- To achieve high bonding strength, the adherend should be polished as much as possible.
- The quality of the bonding joint design determines the bonding strength.
- When the adhesive is used, it can be used immediately after opening the bottle. It must not be left for too long. If it is fast curing, it should not exceed 2 minutes.
- If the adhesive has high strength and fast curing, it can be heated according to the situation. When applying the glue, it should not be too thick. Generally, 0.5mm is better. The thicker the bonding effect, the worse the bonding effect.
- When bonding objects, it is best to apply pressure or fix them with a clamp.
- To make the strength higher, it is best to leave it for 24 hours after bonding.
- One-component solvent-based or water-based adhesives must be stirred evenly when used. After reading this article, if you have questions about adhesives or want to share your knowledge of adhesives with Hopson, feel free to contact us.
Hopson is a professional Chinese adhesive supplier, and it is an honor to meet the global adhesive practitioners here.